ORA-3
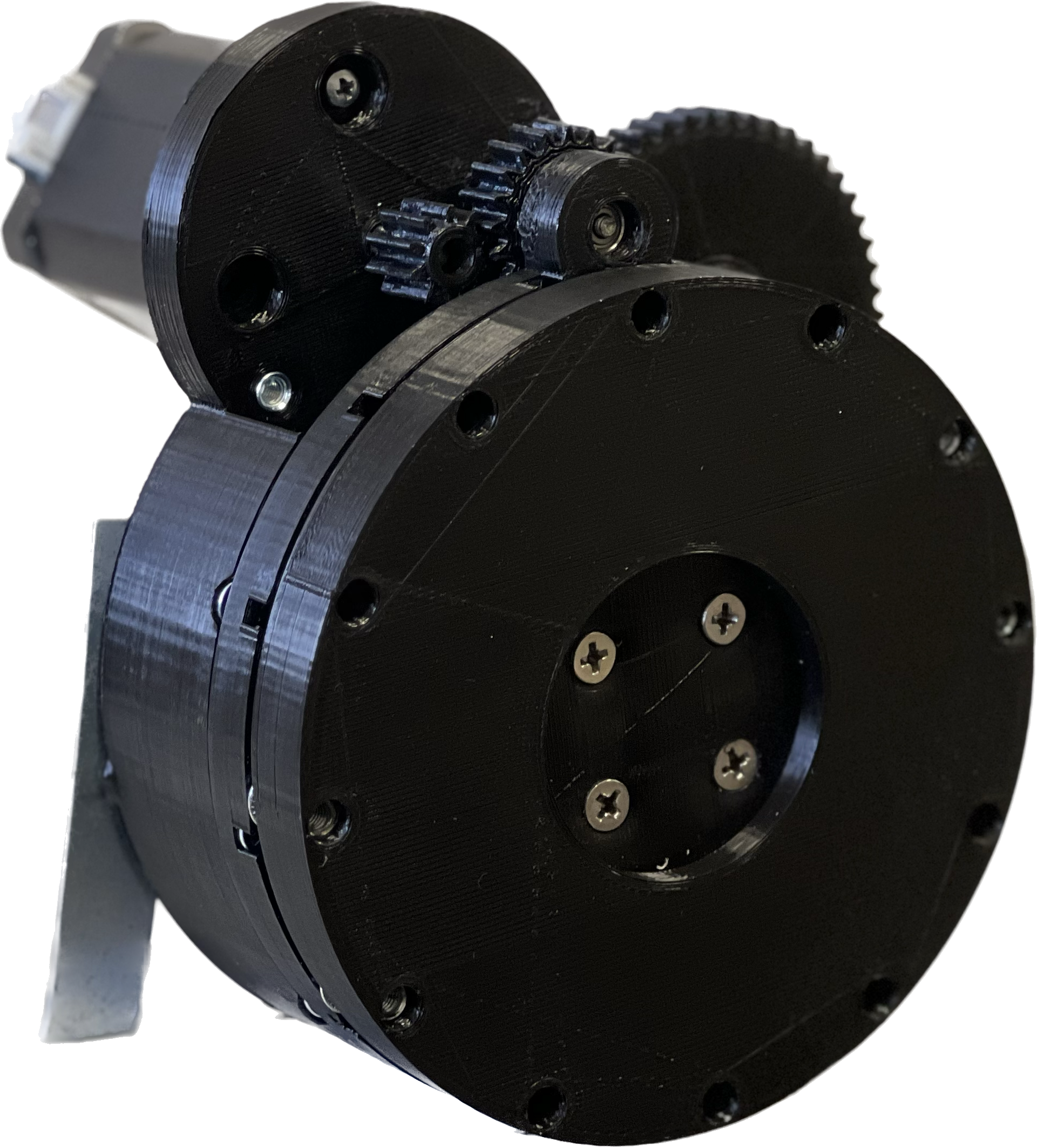
Made for DIY and Prototyping
3d printable Open Robotic Actuator. Designed for DIY and Prototyping purposes. Contains the minimal number of non-3d printed parts. Among the required non-3d printed parts are just bearings, screws and threaded rivets, widely available on any market.
High-Torque
With 1:80 input/output torque ratio the actuators ensures the torque of 6.5 n*m for Nema 17HS4401 stepper motor or 10.5 n*m for Nema17HS6001 stepper motor. That is enough to build the robotic manipulator with 500-600 mm reach and 0.5kg of payload.
Closed Loop
The actuator is designed to use AS5600 12-bit absolute position Hall Effect encoder, that helps to keep track of the actual position of the actuator. This allows to programmatically compensate the mechanical deformation and backlash, determine when the actuator stucks due to excessive load or train the manipulator by moving it with your hand.
Open-Source
The Arduino and python source code for the firmware and the python library required to programmatically control the actuator are available on github.
Open-Architecture
The FreeCad 3d design files, bill of materials and assembly instructions are available here:
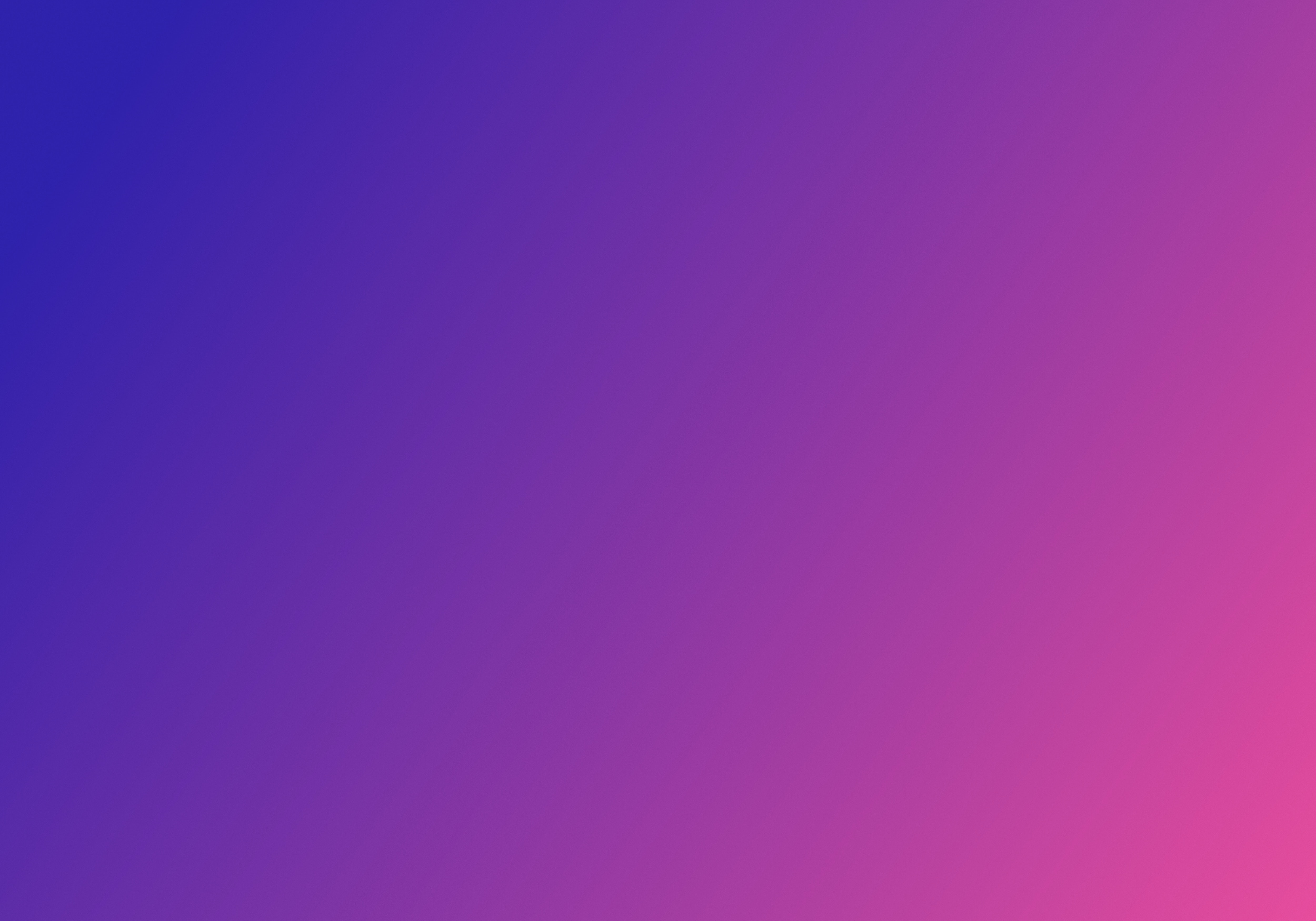
Characteristics
Ratio | 1:80 |
---|---|
Max Torque | 10.5 n*m |
Efficiency | 60 % |
Motor Type | Nema 17 |
Input Shaft Diameter | 5 mm |
Output Shaft Diameter | 45 mm |
Dimensions | 150 x 120 x 55 mm |
Weight | 280 g |